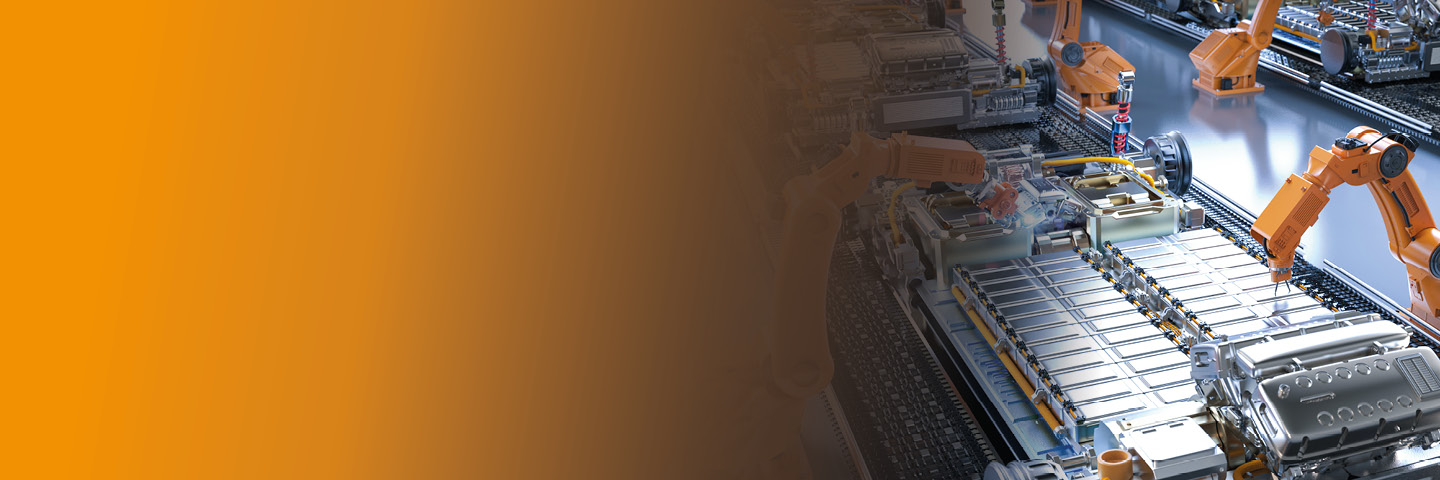
Our X-ray and CT inspection solutions allow you to uniquely visualize the inside of your battery without the need to open them. Find out which one suits you best, whether it's a cylindrical, pouched or prismatic cell. We are known for our commitment to customization, addressing unique challenges with tailored solutions. Regardless of the complexity or scope of the inspection requirements, our adaptable approach ensures that no challenge is deemed insurmountable.
Be able to deal with cathode/anode overhang, foreign particles, deflects, delamination, electric defects, inclusion and/or porosity. Battery cells - whether cylindrical, pouched or prismatic cells - face greater quality requirements due to an increasing number of layers and higher density. Battery modules face higher inspections requirements due to new assembly methods for even tighter packaging of multiple cells in one battery module. And the new battery system designs to latest cells in pack designs lead to new quality challenges.
With hundreds of features inside a battery that can be measured, our technologies provide a comprehensive assessment. This includes dimensional measurements, structural evaluations, and other critical parameters that impact battery quality.
VCbattery's technologies excel at detecting a wide range of defects across various applications in the electric vehicle (EV) industry. Our capabilities span the entire value chain and lifecycle of a battery, offering support from laboratory testing to production, second-use scenarios, and recycling. Here are some specific defects and features that our technologies are particularly adept at finding.
1. Overhang Inspection
Our high-performance 3D inline solution enables the automated analysis of Cathode/Anode overhang, ensuring precise measurements and identifying any deviations that could impact battery performance.
An overhang (the CAT) is already checked in every cell production today, but with severely limited accuracy and high error rates because only 2D X-ray technology is used in-line. The positioning of cathode and anode must be uniform and within defined metrological limits. If the overhang deviates from the tolerance, the performance and safety of the cell is not guaranteed. Using the measurement evaluation, the stacking accuracy can be checked in good time during production in order to intervene in the value chain as quickly as possible.
2. Foreign particles
The requirements for technical cleanliness are one of the most crucial criteria for the quality and performance of every cell manufactured. Foreign particles can occur at various points in the mechanical cell manufacturing process and enter a cell. It is possible that they have gotten in before, during the mixing process. Electrode material from production and contamination caused by welding the cell can lead to damage and limited performance of the cell. It is therefore important to specifically detect these particles and reliably within the process. Using CT analysis and the associated localization of the particle, it can be decided whether it is critical or non-critical.
3. Delamination
Delamination can occur during the coating and subsequent drying of the cathode-anode material, as well as the further mechanical production process of a battery cell. Delamination happens when the coating on the cathode or anode partially lifts or comes off completely, meaning that a uniform flow of electrons is no longer guaranteed. This results in poor performance or possibly damage to the separator. Damaged cells in production must be specifically identified and classified in order to avoid costly recalls or failures in the field. On the way to achieving the decarbonization goals, the detection of this error is a crucial criterion for the reuse of the cells, 2nd use.
4. Porosity of welds
Another key process in battery cell production is welding the cells. They must be hermetically sealed from the environment. There are clear guidelines for acceptable error sizes. The use of traditional, conventional testing methods is time-consuming and not inline-capable but is usually an outsourced process in quality assurance. An inspection of the weld seams using CT technology for pores and voids, provides security and reliable information about changes within the production process. Exact quantification, localization, and subsequent classification according to known standards can be carried out and help to avoid costly product failures.
5. Raw materials - Powder Analysis
The properties and performance of a battery are influenced by a variety of parameters. The correct selection and quality as well as purity of the raw materials used, is an immensely important issue in cell production for reasons of sustainability alone, given the scarcity of raw materials. Using high-resolution computed tomography, the shape and size of the individual grains can be analyzed and determined, from which a distribution of the microstructure can be derived.
We offer a variety of services throughout the entire system life cycle to keep the machines running efficiently and with the highest uptime. Our work team is highly trained to seek the best benefits for your company.
On-Call Service:
Contact us 24/7
Software:
All software updates and upgrades fit seamlessly into the VC ecosystem, and can be tailored to your requirements
System Qualification:
We help you getting your VCbattery system qualified according to your requirements.
Remote Support:
A team of skilled service engineers and software developers is available for immediate help
Retrofits:
We offer comprehensive retrofit upgrades from X-ray component replacement to automation of complete systems
Preventive Maintenance:
Avoid dead capital, we provide you with parts on demand.
Extended Warranty:
We offer prolonged warranty packages for 12, 18, or 24 months.